Soufflenheim Culinary Pottery
Buying our pottery is good, but understanding how it is made is better! Discover below the 10 main stages of manufacture specific to the Siegfried-Burger andamp; Fils pottery. You will discover a stage that is dear to us because it improves the quality of the pottery significantly. It is the "Biscuit" stage, but please note that you cannot eat it. Enjoy your reading !
1- Preparation of the clay
Our pottery is made from a mixture of clays that we prepare in the pottery itself.
This clay complies with European food standards and allows us to make lighter pottery, which is more practical for everyday use, while resisting repeated use in the oven, microwave and dishwasher.
|
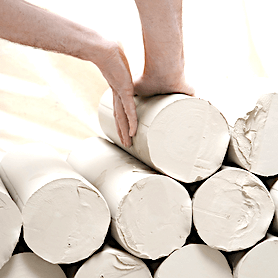 |
2- Pressing / Shooting
The clay strands are cut into disks of varying sizes depending on the piece to be made.
These are then turned or pressed into plaster moulds made by our modellers to give shape to the multitude of potteries we offer.
|
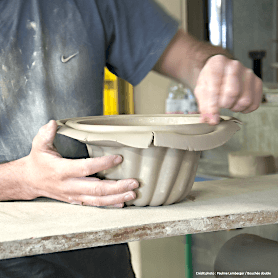 |
3- Drying
Depending on the size of the piece, the drying process can take from 1 to 4 days before moving on to the next step.
To speed up the process, the parts can be stored in the dryer and in this case the drying time is reduced by half.
|
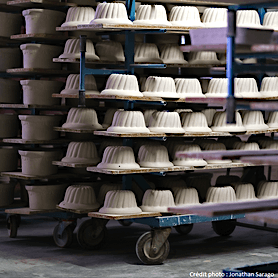 |
4- Cleaning
It is first carried out with a knife to remove any "seams" that may have formed during pressing, then with a sponge to smooth out any imperfections.
|
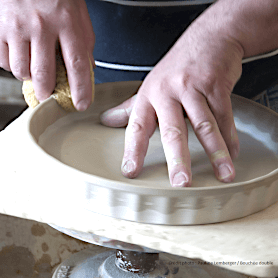 |
5 - Base colour
Called "Engobage", this stage consists of applying a layer of colour by dipping (in a colour bath) or using a paint gun in a spray booth.
|
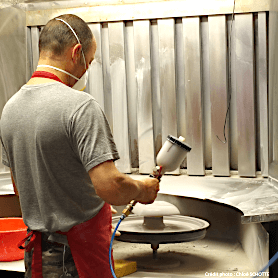 |
6 - Decoration
The patterns are applied to the piece with a pear. The pear is topped with a needle from which a mixture of liquid clay and dye flows.
|
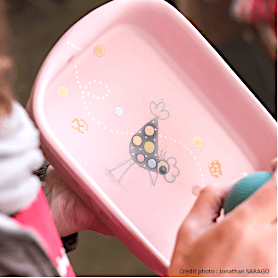 |
7 - First firing
This is called the "Biscuit".
The potter has chosen to adopt the double firing method. This method makes it possible to obtain less porous, more resistant and durable pottery. During this first firing, the pottery is fired for 9 hours at more than 1000 C°.
|
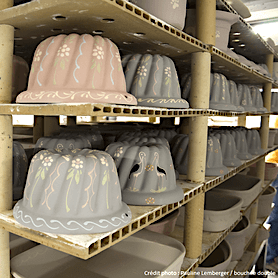 |
8 - Enamelling (lead-free)
This is an essential step, as it is the enamel that will allow the colour to develop and give the piece its shine.
As for the base colour, the enamel is applied by spraying or by dipping in an enamel bath.
|
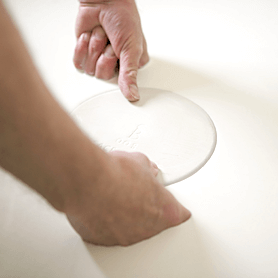 |
9 - Second firing
As for the "biscuit", the pieces are put back into the kiln and fired for 9 hours at more than 1000 C°. During this firing, the magic happens, the white glaze that covers the pieces becomes transparent and shiny to give the pottery all its brilliance.
|
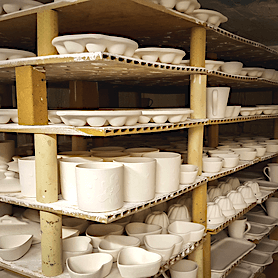 |
10 - Finish
From the preparation of the clay, to the exit of the kiln, a pottery is handled between 10 to 13 times.
At each stage, each of our employees gives a part of themselves with their skills and knowledge to make pottery that we hope will meet your expectations in terms of aesthetics as well as daily use.
As with the base colour, the glaze is applied by spraying or dipping in a glaze bath.
|
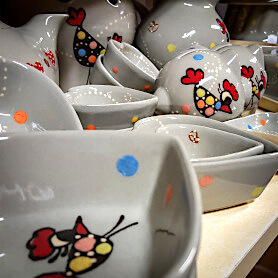 |
Latest comments